Methods for Preventing Turbine Blade Erosion
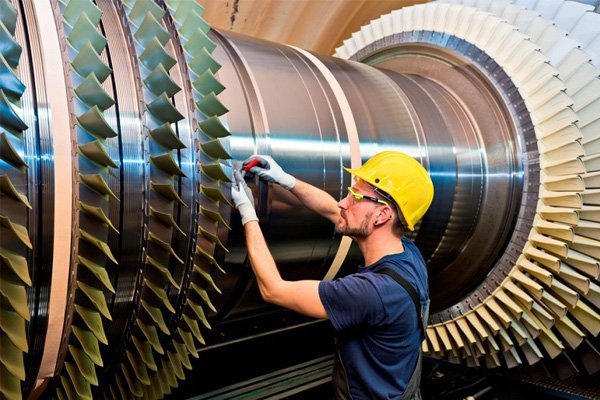
Turbine blade erosion is a significant issue in both gas and steam turbines, leading to reduced efficiency, increased maintenance costs, and potential failures. Erosion occurs due to various factors such as high-velocity particles, moisture, and thermal stresses. Implementing effective prevention methods is essential for prolonging the lifespan of turbine blades and ensuring optimal performance. Below are key methods for preventing turbine blade erosion.
Material Selection and Coatings
One of the most effective ways to prevent turbine blade erosion is through the use of high-strength, erosion-resistant materials and protective coatings.
- Superalloys: Turbine blades are often made from nickel-based or cobalt-based superalloys, which provide excellent resistance to high temperatures and mechanical stresses.
- Protective Coatings: Special coatings such as thermal barrier coatings (TBCs) and erosion-resistant ceramic coatings help protect blades from environmental damage. These coatings enhance durability and reduce the impact of erosive particles.
- Carbide and Nitride Coatings: Tungsten carbide and titanium nitride coatings provide additional hardness and improve resistance against particle erosion.
Air Filtration and Particle Removal
Contaminants such as dust, sand, and other particulates contribute significantly to erosion. Implementing advanced air filtration and particle removal techniques can help mitigate this issue.
- High-Efficiency Filters: Using high-quality air intake filters in gas turbines helps reduce the entry of abrasive particles.
- Inlet Fogging Systems: These systems help capture and remove fine particles before they enter the turbine.
- Cyclonic Separators: These devices use centrifugal force to remove larger particles from the intake air before they reach the turbine.
Optimized Blade Design
The design of turbine blades plays a crucial role in reducing erosion.
- Aerodynamic Profiles: Designing blades with optimized aerodynamic profiles helps minimize the impact of high-velocity particles.
- Leading-Edge Reinforcements: Adding reinforcements or thicker coatings to the leading edges of blades enhances their ability to withstand erosion.
- Self-Healing Materials: Research is being conducted on self-healing materials that can repair minor erosion damage automatically, extending blade life.
Control of Steam and Moisture Content
For steam turbines, moisture content is a major contributor to erosion, particularly at the last stage of expansion where water droplets form.
- Superheating Steam: Increasing steam temperature to maintain a dry state prevents condensation and reduces droplet impact erosion.
- Water Separation Techniques: Installing moisture separators before steam enters the turbine helps remove excess water droplets.
- Drainage Systems: Proper drainage systems ensure that condensed water is efficiently removed from the turbine path.
Erosion Shields and Blade Tip Protection
Installing erosion shields and blade tip protection mechanisms can significantly reduce the effects of erosion.
- Replaceable Erosion Shields: These are sacrificial shields attached to blade surfaces to absorb the impact of abrasive particles.
- Blade Tip Hardening: Special heat treatments and coatings applied to blade tips enhance their resistance to erosion.
Optimized Operating Conditions
Proper turbine operation and maintenance can help minimize erosion over time.
- Startup and Shutdown Procedures: Following controlled startup and shutdown procedures prevents sudden thermal shocks and reduces stress on turbine blades.
- Load Management: Avoiding excessive load fluctuations helps maintain steady-state conditions and reduces wear.
- Regular Inspections: Conducting routine inspections helps detect early signs of erosion, allowing for timely maintenance and repairs.
Gas Turbine Control Systems in Preventing Turbine Blade Erosion
Gas turbine control systems play a vital role in ensuring the optimal operation of turbines, which indirectly helps in preventing turbine blade erosion. These systems regulate key parameters such as temperature, pressure, and rotational speed, adjusting fuel and airflow to maintain the turbine's performance within safe operational limits. By controlling the conditions under which the turbine operates, the control system reduces the likelihood of extreme stresses that can lead to premature blade wear, such as temperature imbalances or excessive vibrations.
Turbine blade erosion is a common issue caused by factors such as high-velocity gas flow, particulate matter, and temperature fluctuations. To combat this, various preventive methods are employed. Advanced coatings, such as ceramic or thermal barrier coatings, provide a protective layer on the turbine blades, shielding them from the harsh operating conditions that would otherwise lead to erosion. Additionally, air filtration systems ensure that only clean air enters the turbine, minimizing the amount of dust and debris that could wear down the blades over time.
Incorporating optimized operating practices through the control system is another effective method for preventing blade erosion. The control system ensures that the turbine runs at consistent, ideal loads, avoiding sharp fluctuations that could cause thermal cycling or mechanical stress on the blades. Furthermore, regular maintenance and inspection of both the control system and turbine components are essential in identifying early signs of erosion, allowing for timely interventions to prevent further damage and extend the lifespan of the turbine blades. The GE Gas Turbine System (GTS) is a leading solution in the power generation industry, known for its high efficiency, reliability, and advanced technology. GE GTS incorporates state-of-the-art gas turbine designs and control systems that optimize performance while minimizing fuel consumption and emissions. IS220PSVPH1A, IS200TSVOH2B are examples of GE gas turbine control system spares.
Conclusion
Preventing turbine blade erosion is crucial for maintaining efficiency, reducing maintenance costs, and extending the operational life of turbines. By implementing a combination of advanced materials, protective coatings, air filtration systems, optimized blade designs, and regular maintenance practices, the risk of erosion can be significantly reduced. As technology advances, the integration of AI-driven monitoring systems and self-healing materials will further enhance the ability to mitigate turbine blade erosion, ensuring more reliable and efficient turbine operations.
What's Your Reaction?






