How To Identify, Reduce, & Manage Obsolete Inventory
Learn how to identify, reduce, and manage obsolete inventory with actionable tips for businesses in Canada to optimize inventory and minimize losses.
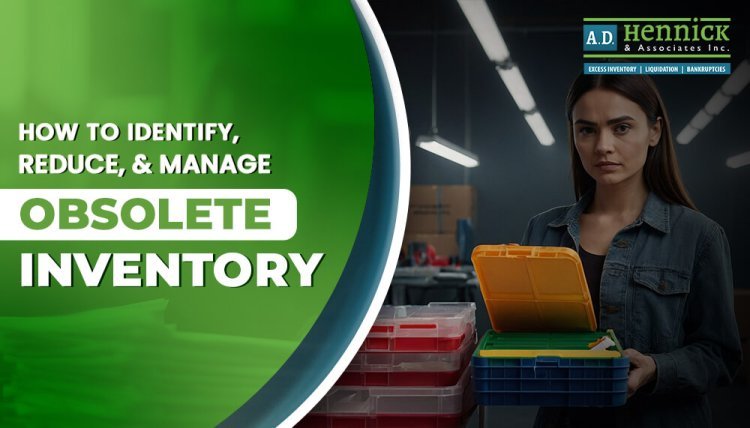
Managing inventory is a critical aspect of running a successful business, but one challenge that many businesses and industries in Canada face is dealing with obsolete inventory. Obsolete inventory refers to stock that is no longer sellable due to factors such as age, changes in demand, or technological advancements. This can lead to unnecessary costs, space usage, and a decrease in overall efficiency. If left unchecked, obsolete inventory can negatively impact your financials and operational performance. In this article, we will explore how to identify, reduce, and manage obsolete inventory, with actionable insights and tips that you can implement immediately.
What is Obsolete Inventory?
Before diving into solutions, it’s important to understand obsolete inventory meaning. Obsolete inventory refers to products that no longer have a market value, either because they are outdated, damaged, or no longer align with customer preferences. This could be due to a change in trends, technological advancements, or a decline in demand for a particular product.
Obsolete inventory examples include:
- Discontinued products
- Products with damaged packaging
- Out-of-date technology that has been replaced by newer models
- Excess stock that no longer aligns with the company’s business strategy
Recognizing obsolete inventory is the first step to effectively managing it, so let’s break down the key strategies for identifying, reducing, and managing these items.
Identifying Obsolete Inventory
The first step to tackling obsolete inventory is identifying it. In many cases, businesses might overlook obsolete stock, which can result in it sitting on shelves or in warehouses for longer than necessary. To identify obsolete inventory, businesses should implement the following processes:
1. Regular Inventory Audits
Conducting periodic audits is the best way to assess your inventory and track which items have not been sold or moved in a long time. These audits should be done monthly, quarterly, or annually, depending on the size and volume of your inventory.
During these audits, focus on the following:
- Sales data analysis: Review sales trends to determine which items haven’t sold in the last 3-6 months.
- Storage time: Items that have been in storage for an extended period may be more prone to obsolescence, especially if they have a shelf life or are technology-based.
- Customer feedback: Sometimes, obsolete inventory is a result of changes in consumer preferences or needs. Gathering customer feedback can help you identify products that may be nearing obsolescence.
2. Inventory Turnover Ratio
The inventory turnover ratio is a key metric that indicates how quickly a business is selling and replacing inventory. A low turnover ratio often signals that inventory is not moving at the expected pace, which could indicate the presence of obsolete inventory.
Calculating the inventory turnover ratio is simple:
Inventory Turnover Ratio=Cost of Goods SoldAverage Inventory\text{Inventory Turnover Ratio} = \frac{\text{Cost of Goods Sold}}{\text{Average Inventory}}Inventory Turnover Ratio=Average InventoryCost of Goods Sold
A low ratio means that certain inventory items are not selling, which could indicate obsolescence.
3. Use of Technology and Software
Investing in an inventory management system (IMS) or enterprise resource planning (ERP) system can greatly assist in identifying obsolete inventory. These systems can flag slow-moving stock, helping you quickly identify products that may become obsolete in the future. Many modern inventory management solutions also offer features for real-time tracking, automatic stock alerts, and predictive analytics to forecast when items are likely to become obsolete.
Reducing Obsolete Inventory
Once you’ve identified obsolete inventory, it’s time to take action to reduce it. Here are several strategies to minimize the impact of obsolete inventory:
1. Liquidation Auctions
One of the most effective ways to deal with obsolete inventory is to sell it off quickly. This is where Top Tips for Attending Liquidation Auctions come in. Liquidation auctions are an excellent opportunity to move obsolete stock at a reduced price to buyers who are looking for discounted goods.
Here are some tips for attending liquidation auctions effectively:
- Research the auction house: Ensure that the auction house is reputable and offers fair terms and conditions.
- Understand the market: Know what your products are worth and set realistic expectations. Liquidation prices will typically be lower than the retail price.
- Set a limit: Be clear on your goals for the auction. Don’t overcommit to purchasing stock that may further contribute to inventory issues.
- Inspect items: Always check the quality of items being sold at the auction to avoid buying products that are even more obsolete or damaged than anticipated.
By attending liquidation auctions, you can sell off products that have been sitting in your warehouse, freeing up valuable space and reducing your inventory costs.
2. Discounting and Promotions
Discounting obsolete inventory through promotions, clearance sales, or bundling offers is another way to reduce surplus stock. Offering discounts on older models, discontinued products, or overstocked items can attract buyers and help clear out space for newer, more in-demand products. Be cautious, though, as aggressive discounting may affect your profit margins. Carefully strategize discounts to ensure they remain profitable while reducing inventory.
3. Donation or Recycling Programs
For products that are truly unsellable or no longer useful to customers, consider donating or recycling them. Many companies donate excess or outdated inventory to charity organizations, which not only helps clear out your stock but can also provide you with a tax deduction. Recycling programs are also an option for products that have reached the end of their lifecycle.
4. Repurposing or Refurbishing
In certain cases, you may be able to repurpose or refurbish obsolete inventory. For example, if you are selling electronic devices, you may be able to update older models with new components and sell them as refurbished products. Similarly, fashion items that are out of season can be rebranded or redesigned to appeal to new customer segments.
Managing Obsolete Inventory Going Forward
Once you’ve taken steps to reduce obsolete inventory, it’s important to put in place processes to prevent it from accumulating again in the future. Here are some strategies for long-term management:
1. Implement an Obsolete Inventory Provision
Businesses should create a provision for obsolete inventory as part of their regular accounting practices. This provision is a financial buffer that accounts for potential future losses from obsolete stock. By setting aside a portion of your budget for obsolete inventory, you can mitigate the financial risk associated with overstocking and better manage your cash flow.
2. Use an Obsolete Inventory Journal Entry
In your accounting system, you will need to record the obsolete inventory journal entry. This journal entry reflects the removal of obsolete stock from your balance sheet, which can help you understand the financial impact of this inventory. It’s important to follow proper obsolete inventory accounting principles when making these entries to ensure that your financial statements are accurate.
3. Optimize Inventory Management
The key to preventing future obsolescence is to improve inventory forecasting and demand planning. By analyzing trends and utilizing predictive analytics, you can better anticipate market changes and stock only what is needed. This involves regularly reviewing sales data, supplier performance, and market forecasts to adjust your inventory levels in real-time.
4. Train Your Staff
Ensure that your procurement, sales, and warehouse teams are trained in recognizing and managing obsolete inventory. This can include regular workshops on how to track and assess inventory, proper stock rotation methods, and best practices for managing slow-moving stock.
Obsolete Inventory Write-Off and Tax Implications
Sometimes, obsolete inventory may need to be written off entirely, especially if it is no longer useful or has no remaining market value. An obsolete inventory write-off can help businesses remove these items from their financial records, but it is essential to follow proper accounting procedures.
In Canada, businesses can claim a tax deduction for obsolete inventory that has been written off, provided they have the necessary documentation. This write-off can offset other taxable income, potentially lowering the business’s tax liability. Be sure to consult with a financial advisor or accountant to ensure compliance with tax laws and to maximize any available deductions.
Conclusion
Dealing with obsolete inventory is a challenge for many businesses, but with proper identification, reduction strategies, and management techniques, you can reduce its impact and free up valuable resources. By conducting regular audits, leveraging liquidation auctions, and improving your inventory forecasting, you can minimize the accumulation of obsolete stock in the future.
Additionally, implementing solid accounting practices, such as creating provisions for obsolete inventory and making obsolete inventory journal entries, will help you maintain accurate financial records. By staying proactive and taking a strategic approach to inventory management, your business will be better positioned to thrive in a competitive marketplace.
What's Your Reaction?






