Common Mistakes in CNC Machine Tool Installation and How to Avoid Them
The arrangement of CNC machine tools is a crucial process that directly influences machining precision, productivity, and the longevity of the equipment. Improper installation may cause misalignment, heightened wear, and expensive downtime.
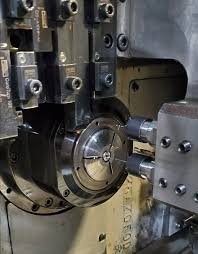
The arrangement of CNC machine tools is a crucial process that directly influences machining precision, productivity, and the longevity of the equipment. Improper installation may cause misalignment, heightened wear, and expensive downtime.
Avoiding and understanding these common mistakes ensures optimal performance and reduces continual maintenance issues. In the following blog, we will outline the specifics regarding frequent errors in CNC machine tool installation and strategies for prevention.
Neglecting CNC Machine Tool Alignment
Proper CNC machine tool alignment ensures precision machining. Misalignment is the cause of inconsistent tolerances, tool breakage, and excessive vibration. Many technicians make this mistake with poor machining accuracy and increased scrap rates.
How to Avoid This Mistake
- Use high-precision measuring instruments such as dial indicators and straight edges to verify machine alignment before and after installation.
- Follow the manufacturer's alignment guidelines and check them periodically for consistency in precision.
Neglecting Foundation and Leveling Requirements
An improperly leveled or insufficient foundation can render the whole CNC machine setup susceptible. Uneven floors that lack sufficient support can lead to structural changes, impacting accuracy and consistency.
How to Avoid This Mistake
- In some cases, be sure to adjust the machine perfectly using precision leveling tools for example machinist levels and laser alignment system.
- Check periodically and adjust levels for environmental fluctuation or floor settling conditions.
Wrong Electrical as well as Pneumatic Connections.
Poor electrical wiring or even pneumatic can cause erratic functions of the machinery and high electricity consumption, among other safety aspects. Most instances of installation problems are due to skipping manufacturer recommendations or using faulty voltage settings during installation.
How to Avoid This Mistake
- Verify that electrical and pneumatic connections comply with the specifications and local regulations.
- Use dedicated circuits with proper grounding to prevent electrical interference and power fluctuations.
- Inspect air supply systems for leaks and ensure that compressors provide the required pressure and flow for the machine’s operation.
Skip CNC Machine Tool Laser Calibration service.
These services are crucial to ensure accuracy in machining operations. Many companies forget to calibrate after installation, which leads to a gradual loss of accuracy and quality control issues.
How to Avoid This Mistake
- Schedule professional laser calibration services immediately after installation to verify and adjust machine positioning.
- Recalibrate machines regularly to maintain optimal performance, especially after relocation or primary maintenance.
- Document calibration results to track accuracy trends and identify potential machine issues before they affect production.
Improper Axis and Spindle Alignment
Misalignment of machine axes and spindles can lead to poor surface finishes, chatter, and excessive tool wear. It is seen when installation teams fail to check geometric accuracy during setup.
How to Avoid This Mistake
- Use laser interferometers or ball bar testing devices for precision measurements to validate the horizontal or vertical alignment of the axes.
- Align the spindles according to manufacturer recommendations, then calibrate the spindle so that it runs out. Proceed to test cuts to validate the optimal alignment for operational work.
Ignoring Environmental Factors
Temperature changes, humidity, and vibrations induced by other machinery can affect the accuracy and lifespan of CNC machines. Most facilities disregard these elements during installation, thereby causing variations in performance.
How to Avoid This Mistake
- Install CNC machines in climate-controlled environments to minimize temperature-related expansion and contraction.
- Isolate machines from excessive vibrations using shock-absorbing pads or placing them away from high-impact industrial equipment.
- Maintain proper humidity levels to prevent rust formation on machine components.
Failing to Perform Initial Test Runs
Not testing runs after installation can lead to missed errors and defects in parts. Many operators consider the installation setup of a machine to be ready for full-scale operations as soon as possible.
How to Prevent This Error
- Conduct a series of test cuts, using a variety of materials, to test the performance and accuracy of the machine.
- Verify that cut dimensions, surface finishes, and tool paths do not deviate before continuing production.
- Change machine settings and readjust parts according to test data.
Inadequate Operator Training and Examination of Reports
Even the best-installed CNC machine would not perform if operators lacked proper training. Many plants shortchange proper training and instead operate the machine improperly, which causes the equipment to malfunction constantly.
How to Avoid This Blunder
- Train operators and the maintenance staff on proper machine setup, operation, and troubleshooting.
- Review installation manuals, manufacturer guidelines, and safety protocols before machine startup.
- Schedule routine maintenance based on documented best practices to ensure long-term reliability.
Poor Cable Management and Safety Considerations
Disorganized cables and improper safety measures can cause hazardous working conditions and increase the likelihood of machine failures. Most facilities fail to consider proper cable routing and safety during the installation of CNC machines.
How to Avoid This Mistake
- Utilize cable trays and protective covers to avoid tangling and accidental damage.
- Install emergency stop buttons and safety interlocks in inaccessible locations.
- Conduct regular safety checks to detect possible hazards and comply with industry standards.
The Verdict
Attention to detail, following manufacturer guidelines, and using advanced methods for alignment and calibration are essential in avoiding common errors in CNC machine tool installation. Properly CNC Machine Tool Alignment and investment in CNC machine tool laser calibration services can make accuracy significantly better, reduce maintenance costs, and prolong equipment life cycles. Manufacturers can achieve maximum productivity while maintaining high-quality machining by addressing installation blunders.
What's Your Reaction?






